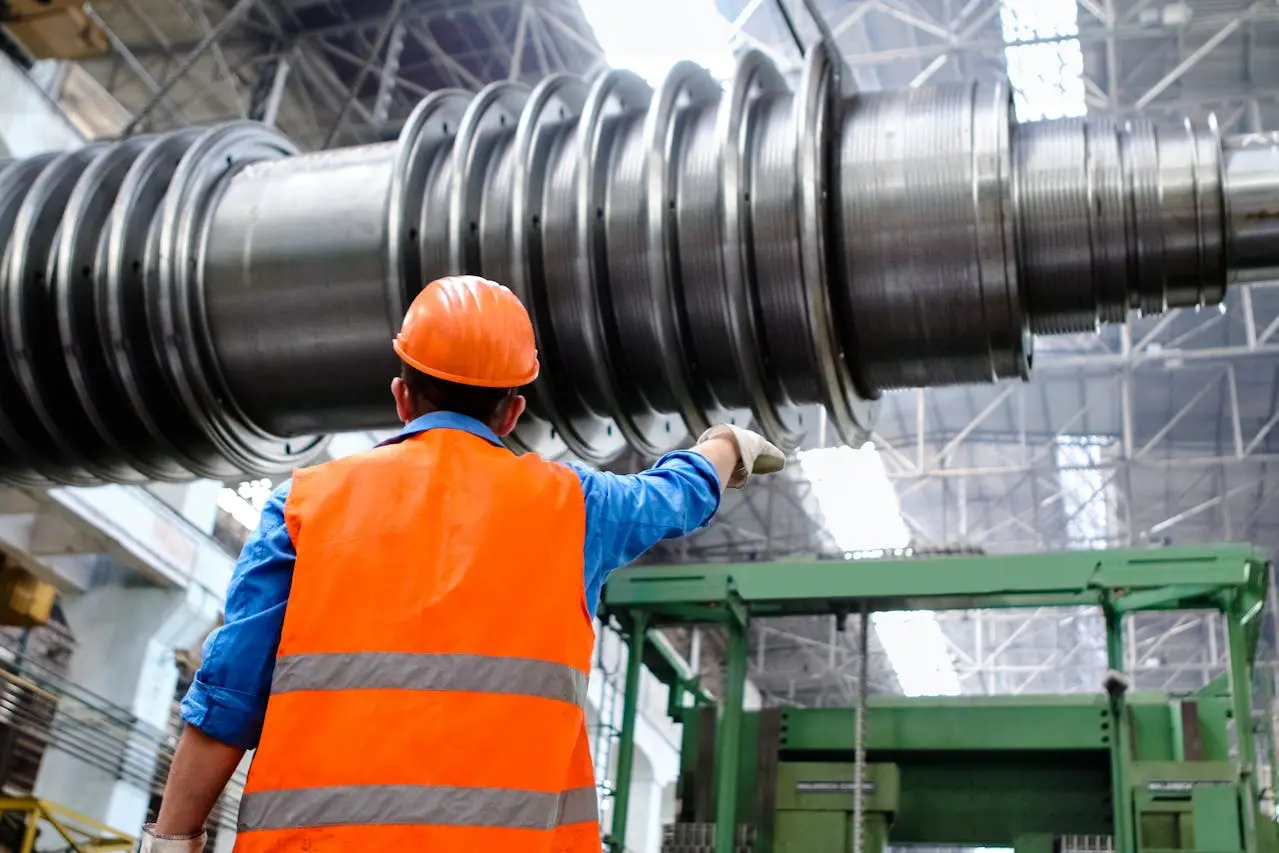
Predictive maintenance has become a game-changer in the production sector, pushing businesses toward more efficient, cost-effective operations by preventing issues before they become expensive problems. Here’s how predictive maintenance is transforming production costs and why it’s becoming a top priority across industries.
What is Predictive Maintenance?
Predictive maintenance uses data from sensors, machine learning, and real-time analytics to monitor the health of machinery and detect signs of wear or potential failure. Rather than waiting for machines to break down or sticking to fixed maintenance schedules, predictive maintenance tells production managers exactly when equipment needs attention, making maintenance proactive rather than reactive.
Key Benefits of Predictive Maintenance for Cost Savings
Reduced Downtime and Increased Uptime
Unplanned downtime is among the highest costs in production. Predictive maintenance reduces downtime significantly by alerting managers to issues before they escalate. With fewer unexpected breakdowns, production lines stay up and running, ensuring output remains steady, making this one of the best energy-efficient solutions.
Lower Repair and Replacement Costs
Fixing minor issues before they become major failures is considerably cheaper. Predictive maintenance prevents the need for costly replacements by catching wear or degradation early, allowing production teams to take quick, less costly action, such as part replacement or recalibration.
Minimized Inventory and Spare Parts
Traditional maintenance models often keep large inventories of spare parts, leading to storage and inventory costs. Predictive maintenance allows for more precise inventory management, as parts are only ordered when needed based on the machine’s current condition, cutting down on inventory costs and freeing up space for other needs.
Extended Equipment Lifespan
Consistently monitoring equipment health means machines receive care only when necessary, minimizing wear and tear. Over time, this proactive approach extends the lifespan of equipment, reducing the need for frequent, large-scale investments in new machinery.
Enhanced Resource Allocation
With predictive maintenance, companies can assign maintenance teams more effectively. Rather than allocating resources for unnecessary inspections, skilled technicians can focus on areas that genuinely require attention, optimizing time, labor, and expertise.
The Role of IoT and Big Data in Predictive Maintenance
The Internet of Things (IoT) and big data analytics are the backbone of predictive maintenance. Sensors on equipment track performance metrics like temperature, vibration, and pressure, sending data to centralized systems for analysis. By leveraging these data points, predictive algorithms can create a comprehensive view of machine health and alert teams to potential issues. This use of real-time data creates a proactive maintenance approach, ensuring that production remains as efficient as possible.
Case Studies of Predictive Maintenance Success
Leading companies have demonstrated substantial cost savings through predictive maintenance. For instance, aerospace and automotive manufacturers have reported millions in savings by reducing downtime and extending equipment life. By minimizing unplanned downtime and ensuring equipment operates at peak performance, predictive maintenance continues to prove its financial worth.
Final Thoughts
For production facilities focused on reducing costs, predictive maintenance is an invaluable tool. Through intelligent monitoring and analytics, businesses can protect their assets, optimize resource allocation, and eliminate inefficiencies. As more companies adopt predictive maintenance strategies, it’s clear that the future of production will be defined by smarter, data-driven maintenance, leading to more streamlined and profitable operations.