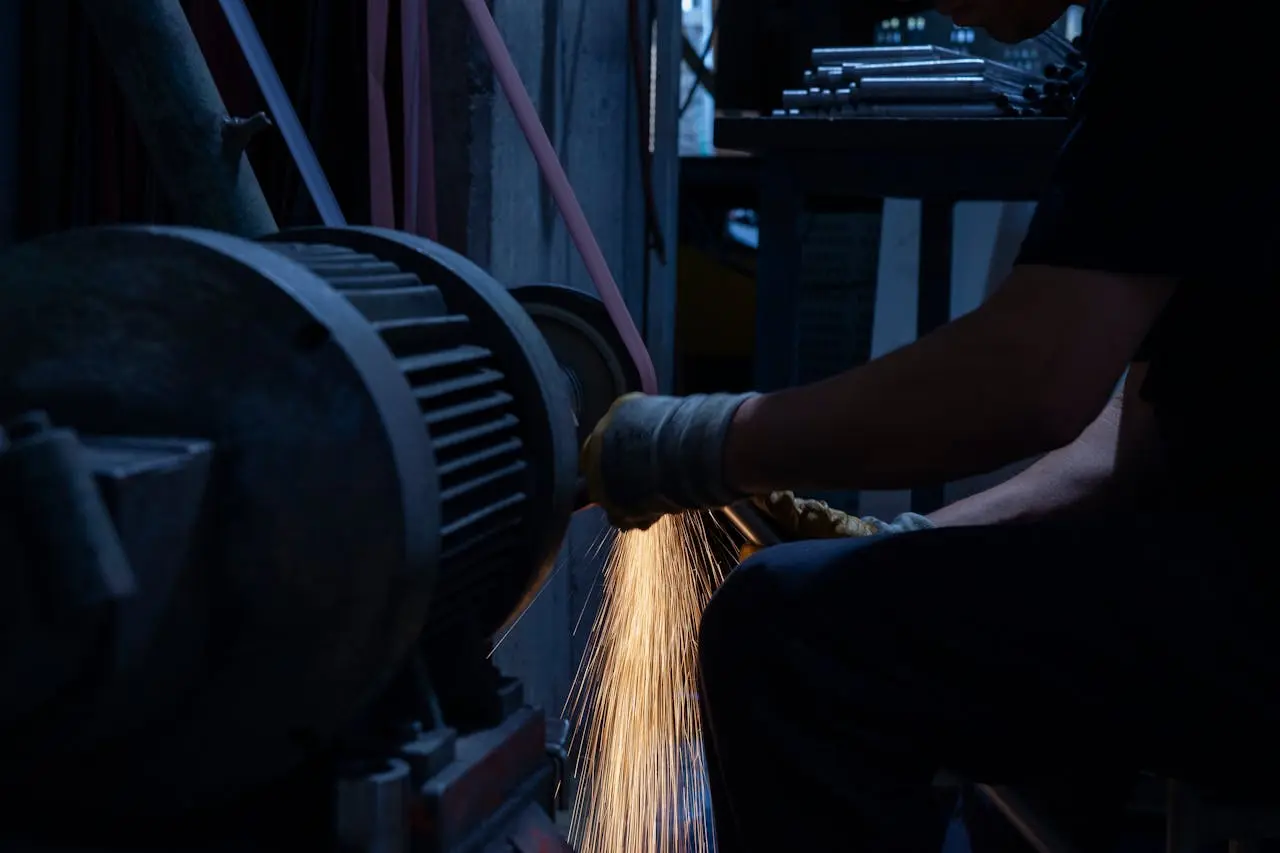
In today’s competitive market, manufacturers face constant pressure to reduce costs, improve quality, and accelerate production. Lean manufacturing has emerged as a powerful approach to meet these demands, offering a systematic way to eliminate waste and boost efficiency.
Originating from Toyota’s production system, lean manufacturing focuses on creating more value for customers with fewer resources.
This blog post will explore the key strategies of lean manufacturing that help companies reduce waste and increase efficiency.
1. Understanding the Types of Waste (Muda)
At the core of lean manufacturing is the identification and elimination of waste, known as muda in Japanese.
Waste is defined as any activity that does not add value from the customer’s perspective.
Lean manufacturing categorises waste into eight types:
- Overproduction: Producing more than what is needed or producing it too early.
- Waiting: Idle time caused by delays, equipment breakdowns, or waiting for materials.
- Transportation: Unnecessary movement of products or materials that adds no value.
- Excessive Inventory: Holding more inventory than is necessary, leading to increased storage costs and potential obsolescence.
- Motion: Unnecessary movements by workers, such as reaching or walking, that do not add value.
- Defects: Production errors that require rework or result in scrapped materials.
- Overprocessing: Performing more work or adding more features than the customer requires.
- Underutilized Talent: Not fully utilising employees’ skills and capabilities.
By recognising and addressing these forms of waste, manufacturers can streamline their operations and focus resources on activities that truly add value.
2. Just-In-Time (JIT) Production
Just-In-Time (JIT) is a cornerstone of lean manufacturing that aims to produce only what is needed, when it is needed, and in the amount needed. This approach minimizes inventory levels, reduces storage costs, and eliminates the waste associated with overproduction.
JIT requires a highly responsive and flexible production system, as well as strong relationships with suppliers. It often involves practices like kanban (a scheduling system for lean production) to signal when new materials or components are needed, ensuring a smooth and continuous flow of production.
3. Continuous Improvement (Kaizen)
Kaizen, or continuous improvement, is a fundamental principle of lean manufacturing that emphasises the ongoing effort to improve products, processes, and services. It involves everyone in the organisation, from top management to frontline workers, in identifying opportunities for improvement.
Kaizen encourages a culture of continuous learning and adaptation, where small, incremental changes are made regularly. These changes, though small on their own, accumulate over time to produce significant improvements in efficiency and quality.
4. 5S System
The 5S system is a method for organising and maintaining a clean, efficient, and safe workplace. It consists of five steps:
- Sort (Seiri): Remove unnecessary items from the workplace.
- Set in Order (Seiton): Arrange tools and materials so they are easy to find and use.
- Shine (Seiso): Clean the workspace regularly to maintain high standards of cleanliness.
- Standardize (Seiketsu): Establish standards for organising and maintaining the workspace.
- Sustain (Shitsuke): Ensure that the 5S practices are consistently followed.
Implementing the 5S system helps eliminate waste related to disorganisation and inefficiency, leading to a more productive work environment.
5. Standardised Work
Standardised work involves documenting the best practices for each process and ensuring that all workers follow them consistently. This helps reduce variation in the production process, leading to more predictable outcomes and higher quality products.
Standardised work also serves as a foundation for continuous improvement, as it provides a baseline against which changes can be measured. By continually refining and updating standardised work procedures, companies can achieve greater efficiency and reduce waste over time.
Utilise These Lean Manufacturing Strategies To Improved Success
Lean manufacturing offers a powerful set of strategies for reducing waste and increasing efficiency.
By focusing on eliminating waste, optimising processes, and fostering a culture of continuous improvement, manufacturers can enhance their competitiveness and deliver greater value to customers.
Implementing lean principles requires commitment and collaboration across all levels of the organisation, but the rewards, such as increased efficiency, reduced costs, and improved quality, are well worth the effort.
[…] These innovations allowed for greater precision, speed, and cost-effectiveness in production, also known as lean manufacturing. […]
[…] Efficiency and Productivity: One of the most significant advantages of automation in modern manufacturing is its ability to boost efficiency and productivity. Automated systems can operate 24/7 without the […]